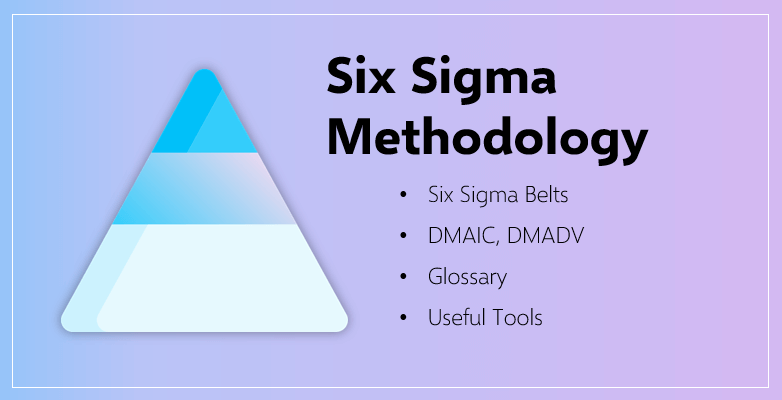
Six Sigma Methodology: Definiton & Complete Overview About It
Everyone strives to improve the quality of their work while decreasing the number of their mistakes and adjusting the time they are spending. Some various methodologies and techniques are constructed to achieve this improvement: There is the Kaizen Methodology which focuses on change, specifically good change. There is the Lean Methodology which is the optimization of resources, effort, and time while improving customer satisfaction. And there is the Six Sigma Methodology.
What is Six Sigma?
As you can see, and you would see if you research every one of these methodologies, they are quite similar to each other. Six Sigma is an improvement process that focuses on reducing waste and errors and increasing the satisfaction of clients for an organization or a business. This method is based on data and analysis to get rid of avoidable mistakes and enhance various techniques from manufacturing through management and employment.
The Goal for the Six Sigma Methodology
The aim for Six Sigma is by advancing the efficiency of different processes throughout a company, each of the output processes will be positively affected by it. This means the accuracy of production will be better; the employees will be more satisfied and determined to do better at their job, and the quality of the finished product will be superior.
As you can imagine developing an improved quality management system is not that easy. The Six Sigma analysis needs to be dependent on the data. Whether employees of the same company are doing the Six Sigma analysis process or not, the members of that research team should be knowledgeable about the method. If the Six Sigma process is not conducted by professionals and professionally, certainly, it will not produce accurate results. That is why specific steps of this operation should be carried out with people who know what they are doing to achieve an almost perfect output for the organization.
This technique not only realizes what a business is doing but also what they can do to improve their business. You can look for and find the Six Sigma methodology around the world and among every industry there is. The reason for that is it can only help a company to do better. And you can see that on the origin of the methodology and its history.
The History of the Six Sigma Methodology
Even though the statistical analysis operations of sigma can date back to the beginning of the 20th century, the company which first applied it was Motorola in 1984. Motorola used this method and subsequent tools to reduce the defective parts in their manufacturing processes at first. And then, when they saw how much the method itself improved the operation, they applied the methodology to other various aspects of their business as well.
In the following years and decades, from small local businesses to huge multinational conglomerates pursued the accomplishments of the Six Sigma methodology. Until the late 1990s, the technique was a concept that was only known by people who were ‘inside the industry’. The method gained popularity and reputation thanks to Jack Welch who was the CEO of one of the biggest companies in history: General Electric.
Jack Welch raised the value of General Electric by 4,000% during his time of being the CEO of the company from 1981 up until 2011. A lot of business executives, coworkers, and Welch himself credited the Six Sigma methodology as the main reason for this increase in worth. General Electric achieved this not only by earning more and generating more revenue but also by saving an incredible amount of money as well.
When Should You Use the Six Sigma Methodology?
Before you apply the methodology, you need to clarify the objectives of your business or projects. By identifying the areas, you want to gain more from via the Six Sigma method and the fields you want to reduce waste, you will be taking the first step.
Project Management
The technique itself is a project management system and additionally, it can prove other project management systems as well, if applied. No matter which field your business operates in and no matter what the size of the project is, you can utilize the Six Sigma method.
Operational Processes
You can use the method if you are focused on operational processes. These can include manufacturing and management of before, during, and after the manufacturing periods. In the pre-production phase of a project, as well as production, several actions need to be taken. The structure of these plans and the execution of all operations need to be managed. Therefore, the Six Sigma methodology comes into place to manage and adjust different aspects of a project.
Waste Reducing
The method can also be used if you are looking for a way to reduce the amount of waste your organization is generating. This waste can be considered as time, raw or processed materials, effort or energy, and various other resources.
Eliminating Mistakes, Errors, and Defects
One other way to use the Six Sigma method is to use it when you are determined to diminish the mistakes, errors, or defective products. However, to achieve that, you need to identify the problems themselves, first. You need to do research, analyze the existing data, and precisely define what has been causing your business to make mistakes, errors, or produce defective products.
Increasing Efficiency
Perhaps one of the main reasons to use this technique is to increase the efficiency of your business. This includes the improvement of productivity not only of employees but also the work itself as well.
Satisfaction of Employees and the Customers
The key result of the Six Sigma methodology is the accomplishment of high customer satisfaction. At the same time, the organization has to keep the satisfaction and the happiness of their employees as well. That is why the Six Sigma technique is useful to maintain a stable satisfaction level.
New Design
This method can be used to analyze processes and designs that do not work and replace them with effective ones. This replacement can be done during all of the processes: pre-production, production, marketing, customer service, and many more.
The Methodologies of Six Sigma
The key principles and applications are carried out by so-called ‘sub-methodologies’. Even though the main aim for them is the same (or at least similar), they hold slightly different qualities in themselves. And although they individually provide different pathways to success and improvement, they take steps for the same goal: Efficiency.
Below, you can find the details of these two methodologies of Six Sigma: DMAIC and DMADV.
DMAIC (Define, Measure, Analyze, Improve, Control)
DMAIC mainly focuses on making existing processes of the organization better. It is the most popular sub-methodology and DMAIC comes to mind when someone talks about the Six Sigma methodology. Let’s analyze each of the letters of the acronym and give details on them:
D is for defining the specific needs and requirements the customers ask for to the organization. The goals of the projects can also be considered to match the needs of the clients.
M is for measuring the main characteristics of existing processes. The ‘M section’ is for the team of members to realize and recognize the organization, research, and collect data.
A is for analyzing the collected data from the organizations. The 80/20 rule can be considered in this section. Targeting the crucial accomplishments which make the most of the impact for the organization.
I is for improving each of the processes. This section focuses on testing every employee’s work and works on verifying this work on the project. The team of members who are using the Six Sigma method has to confirm each of the improvements to see if they worked or not.
C is for controlling the methodology in the future to maintain a low level of errors in the organization. If you have completed the technique in one project and minimized the errors, you need to keep this process going on future endeavors in the company as well. Once you have accomplished your goal, work on sustaining it for every project and each of the departments.
DMADV (Define, Measure, Analyze, Design, Verify)
DMADV focuses on introducing new processes to the Six Sigma methodology. It develops new products to work with the technique. As with DMAIC, let’s analyze the acronym itself:
D is for defining the goals of customers and the organization.
M is for measuring the qualities of the company that is Critical To Quality (CTQ). These include the capabilities of each of the products, services, or projects; the process capability of the manufacturing machinery, and the risks the organization takes in general.
A is for analyzing the information gathered from the measuring processes.
D is for designing new processes and optimizing services based on the analyses made in the previous step of the process. This is the defining section and step of this sub-methodology.
V is for verifying the newly made designs with a so-called ‘trial run’. The Six Sigma methodology is successfully implemented to new designs, processes, products, and services and then, provided to the organization. These products subsequently are offered to customers, clients, and buyers in general.
What Are the Benefits of the Six Sigma Method?
The Six Sigma methodology, while improving the business and managerial processes of a company, also improves the individuals who are applying this method as well. Let’s look at some of the advantages of the Six Sigma method:
Eliminating ‘Gut Feeling’ Decisions
If you are not well informed about the data your company holds, you will be making decisions based on your gut feeling. That is a harmful way to operate a business, no matter how big or small it is. The analysis with the Six Sigma method removes the possibility to continue your decisions with solely your assumptions. The data you gather and the subsequent analysis period ensure an improved decision-making process. That is the only way you can make objective decisions to solve problems and be better at your job.
Establishing a Qualified Team
The success of this technique relies on the team effort of the team of members. The ‘team effort’ phrase is important here since ‘individual effort’ for this process will not be enough to accomplish anything. You need to create a team that the members of it can voice their concerns and opinions and work well together with other departments and other team members. That way the Six Sigma method will be improving the collaboration and communication among your departments in your company as well.
Improving the Quality
Perhaps the best benefit of the Six Sigma methodology is the enhancement of every process. The utilization of this technique can improve periods from gathering up raw materials to customer service after the product has been delivered.
Customer Satisfaction
The quality of your final product or service will also determine the satisfaction level of your customers. Think of all of these processes as dominoes. If you apply the Six Sigma method to even only one of the dominoes, they will end up positively affecting one another. And the customers’ experience with your product or service is the last domino which is the most important one.
Removing Waste
Better quality management combined with improved time management will result in cutting down the waste you are generating. These waste, errors, mistakes, or defects can be considered as wasted time, wasted effort or energy, wasted personnel, or even wasted potential of a product or a service.
Increasing Productivity
If you thoroughly go through the crucial datasets of your company, you will be more planned than ever for your next product or service. Planning with efficient strategies will lead your organization to become more productive. You can not only better the productivity of your employees but also can increase the level of production as well.
The Belts of the Six Sigma Methodology
Are you familiar with karate? Are you familiar with the belts of the sport that demonstrate the level of expertise and training? The belts of the Six Sigma methodology are the same! Let’s count down the hierarchy of the mastery of training and experience:
Executives
The leadership at the top is the one who is in charge of the whole operation. The CEO, board members, and executive staff initiate the implementation of the Six Sigma methodology. Following that, they are the group that oversees the entire process of the application of this method as well.
Champions
Champions ensure that the operation goes smoothly. For example: If the executives are the owners of a restaurant, champions are the managers. They interact with each of the employees and mentors them in their training. Champions are specifically selected by the executives.
Master Black Belts
Champions carefully select the individual Master Black Belts. And they are mentored by Champions as well as they are trained for the Six Sigma method. Master Black Belts mentor and train the employees who are on a lower level of expertise. They are also responsible for determining possible projects to apply the Six Sigma method.
Green Belts
Green Belts take charge of the projects that Master Black Belts select for the application of the Six Sigma methodology. They often lead these projects, but they always report to Master Black Belts.
Yellow Belts
Yellow Belts do not have a deep knowledge of the method such as Master Black Belts or Champions do have. Even though they do not have an intricate understanding of the processes, they contribute to projects.
White Belts
White Belts are the recruits to the Six Sigma methodology. They might know what the concept means; however, they do not need to do any training or testing to achieve this color of the belt. The certification of it can take only a few hours and it is the first belt of the chain.
Certifications for the Six Sigma Belts
Anyone can apply to get a certification to get one of the Six Sigma belts, but there is not only one organization that offers these certificates. There are many different organizations with different application processes. Other schools and private companies can offer quite different steps to acquire the necessary certificates.
Even though there is no one single way to acquire it, they surely require a certain set of skills and the basic level of knowledge of the Six Sigma methodology. You can apply for it online or through a business school as well. The training for it can be done in various places and through various stages.
The training for the Six Sigma method can be learned in an office with experts; it can be learned by those same professionals onsite; you can learn it by yourself online or you can utilize the combination of all of them. Certificates are usually given after the candidate passes the written test.
What Can A Certificate for the Six Sigma Method Do For You?
A certificate can be easily disregarded when you are applying for a job position. Let’s say you are applying for a business analyst position in a medium-sized company. You can bring a lot of certificates from various events and NGOs that you earned to the interview, but they would not be enough for you to secure the job position. But a Six Sigma certificate is different…
This certificate shows your potential employer that you are good at improving your performance, your coworkers’ performances, and the quality of the company for which you are working. It is not only a piece of paper; it actually holds weight and says ‘I am qualified to improve the job I do’. So, what can this mean for you?
It can help you stand out among other candidates. Even if you are happily employed, you can earn a higher salary and can be considered for higher job titles, positions, and promotions in general. It is not a necessary means for you to climb the ladder of success and it can be expensive to follow the steps of the Six Sigma method. Every belt means more training and more work, which not only costs you time but also money. You do not have to do it… but if you do, then be sure that it is incredibly useful.
The Six Sigma Glossary
Below, you can find some key concepts and useful terms used in the methodology:
7 Wastes: This (originally Japanese) concept looks for the wasted resources in the areas of transportation, inventory, motion, waiting, overprocessing, overproduction, and defects of a company.
Acceptable Quality Level (ACL): This level of quality refers to the standard that is set. The products and services should meet the standards of ACL.
Checksheet: It is a chart that collects data over time. It is a ‘must-have’ tool in every Six Sigma process to keep track of the occurring problems.
DPMO: The DPMO acronym refers to the number of Defects Per Million Opportunities.
DMAIC
DMADV
Critical To Quality (CTQ)
Kaizen Methodology: As it was mentioned at the beginning of this blog post, it is a Japanese concept focused on continuous change and improvement similar to Six Sigma. You can find detailed information on this blog post here.
Tollgates: Between every step of the application of the Six Sigma method there are waiting and reviewing periods. These periods are called ‘tollgates’.
Value Target: The organization’s financial goal for the project, which uses the Six Sigma method for, is called the ‘value target’.
SIPOC: Standing for Suppliers, Inputs, Process, Outputs and Customers, the SIPOC methodology tries to build a process map to make an overall analysis of the business. Someka provides SIPOC Excel Template to help you use this method. You can also download SIPOC Google Sheets template if you prefer an online file.
Useful Tools for Applying the Six Sigma Technique
Kanban Board
The Kanban system allows your project to go smoothly while maintaining the sustainability of it from start to finish. It is a visual tool to maximize your workflow as well as minimizing your wastes. You can download and start using a Kanban Board right inside Microsoft Excel. By using Someka’s Kanban Board Excel Template, you can not only convert all of your Six Sigma principles into visual, colorful, and customizable tables and charts but also keep track of your project. If you want to use it online, you can also download Kanban Board Google Sheets Template.
The 5 Whys
This technique is not actually a tool you can download or make to use. You can do it with a piece of paper and a pen or you can even do it in your mind! If you are having trouble getting into the deep details of a problem and finding its root cause, you can use this technique. Just ask 5 following ‘Why?’ questions, respectively. For example:
- Why did our product fail?
Answer: Because the customers did not like it.
- Why did the customers not like the product?
Answer: Because we changed our design.
- Why did we change our design?
Answer: Because our budget was cut.
- Why was our budget cut?
Answer: Because the company did not make enough profit last year.
- Why did the company struggle to make a profit last year?
These 5 Whys will lead you to the cause of your problems. If you think that you did not get to the real reason for your problem, you can always use ‘5 more whys’.
It’s very easy to make this analysis with Someka’s ready-to-use 5 Whys Excel Template. No installation needed, you can download and start using it.
If you want an online tool, then you can download Someka’s 5 Whys Google Sheets Template. You can work from any device with colleagues simultaneously.
Pareto Chart
The Pareto Principle focuses on the 80/20 rule. It is the concept that a small number of actions, people, or decisions (20%) are so important that they make the most impact overall (80%). This analysis is presented with a Pareto chart which consists of a bar and a line graph. Someka has a very helpful Pareto generator template in its portfolio: Pareto Chart Excel Template. This tool will automatically build a pareto chart according to your input data. You can also download Pareto Chart Google Sheets Template if you want to use it simultaneously with your colleagues.
How Can You Use Someka Templates for the Six Sigma Method?
Six Sigma Templates
Someka has six sigma calculators to help you define six sigma levels and create process charts dynamically. You can download 6 Sigma Excel Template or 6 Sigma Google Sheets Template for a ready-to-use calculator.
Gantt Chart Maker
You can use Someka’s incredibly detailed and comprehensive Excel Gantt Chart Maker to calculate how much time it will take for each of the processes. This automatically generated Gantt chart combined with the Six Sigma methods and its stages will create the ideal for you to approach every project of your organization. It will be your essential tool to keep track of time, actions, and individuals related to your project and organization in general.
Automatic Flowchart Maker
You can also choose to use flowcharts for your Six Sigma methods as well. Someka’s Automatic Flowchart Maker shows you the workflow of all of your systems running throughout your organization. It summarizes each of the processes, projects, and analyses to make you realize and understand every concept better. And with the click of a button, it creates customizable, colorful, and professional-looking flowcharts for you.
Flowcharts work together with the Six Sigma method in that flowcharts show the progress for each of the processes. You can keep track and easily follow them in the flowcharts created for you.