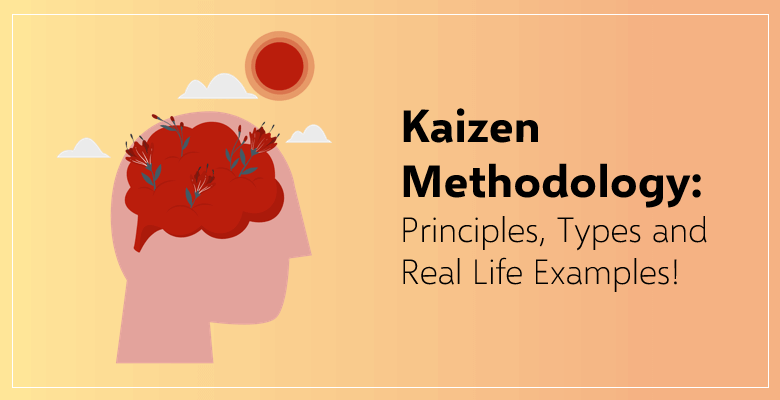
Kaizen Methodology: Real Life Examples that Wikipedia Can’t Tell You
Table of contents
- What is the Kaizen Methodology?
- The Different Types of the Kaizen Methodology
- Why the Kaizen Methodology Is Important
- How to Implement the Kaizen Method to Improve Your Business
- Real-Life Examples of the Kaizen Methodology
- How the Kaizen Methodology and Someka Excel Templates Work Together
What is the Kaizen Methodology?
Kaizen methodology is an approach to continuously improve the work, the work environment and the workers. The basic core of the method centers around the collaboration and the communication between the employees and the work they do together. Its main purpose is to diminish any potential risks and problems; increase the level of productivity, bring a positive attitude to the workplace and innovate.
The word itself is Japanese and it is the mix of two words. ‘Kai’ means change and ‘zen’ means good and better. Therefore, the translation of the word “kaizen” can be thought of as ‘good change’ or ‘change for the better’. Even though its principles and philosophy go back to Japan after the Second World War, the term was popularized by Masaaki Imai. Imai’s 1986 book titled ‘Kaizen: The Key to Japan’s Competitive Success’ brought the concept to the West and popularized it outside of Asia.
Earlier Japanese success principles relied on two key factors: Gradual improvement and respect for people. This set of principles, values and behaviors were used in the Toyota Motor Corporation as well. These ideas became popular in the manufacturing world for those who wanted to follow the footsteps of successful manufacturers. This concept was later coined ‘The Toyota Way’ in 2001.
The Kaizen Strategy
The strategy itself relies on the fact that small yet crucial changes and adjustments over time are going to bring amazing positive results. The key to applying this strategy and succeeding by using it is to ‘execute the strategy routinely’ and to ‘work together’. It is actually a guide on how to implement changes in your business and organizations. The Kaizen belief suggests that everything can be improved if it is worked on. This positive ‘take action into your hands’ approach can and should work if (and only if) it is accepted in an ‘organizational way’.
This means if you are managing a business and only five of your employees apply Kaizen principles into their work, the Kaizen method will not work as it is supposed to be. From the President of the company to the CEO and to the new interns, everyone should be aware of the method. They should apply its principles and the method itself with different types of approaches. In addition to applying it, they should be operating without any excuses. In order to achieve a ‘positive change environment’ at the workplace, every employee (from the CEO to each of the employees) should be focused on improving the work.
No matter how many problems there are and no matter how big or small they are, every problem is an opportunity for a success story. Thus, regardless of the size and the impact of the change you are providing, change will always be for the better.
The Culture of Improvement
Because the Kaizen methodology is based on constant improvement, it happens to create a strong culture at the workplace as well. Without the growth and improvement of each of the employees, the growth of the company will not be possible either. This growth can be considered as an economic, cultural or even physical. How can you expect to grow as a business, if your employees and you do not wish to improve yourselves?
Therefore, the people who are applying the Kaizen method at their workplace should not work only for their company. They have to work for themselves and in themselves as well. They must improve their abilities, attitudes and approaches to life and work in order to grow as an individual. And only then, they will be able to help improve their organizations.
The Kaizen methodology also comes with a series of recommendations and principles to follow. By using these as your practical guide, you can apply the method for yourself and for your work at your workplace in an easier way. One of these elements is the ten principles that the Kaizen philosophy is based on.
The Kaizen Principles
These principles can be considered as the ‘mindset’ you should be following while working:
Think outside the box
Conventional ideas are called ‘conventional’ because of a reason. These fixed points are not going to challenge you or any of your coworkers, supervisors or bosses. They are the opposite of change. That is why if you want to apply the Kaizen method and the change that comes with it, you should always think outside the box.
Locate problems and work on solving them
Try to find the hurdle between you and your goal. Locate the exact problem forcing you to fail… and solve it. Evaluate the situation and figure out a way on how to solve the problem. Work on the problem, execute the solution and improve on the situation.
Avoid perfectionism
Try not to seek perfection on everything you do, because ‘perfect’ does not exist. You decide on whether anything is perfect. And you will find that nothing is perfect. Your attitude should be adapting the changes, not wait and dwell on perfectionism. It will waste your time and others’ as well. Do any work as best as you can and as early as you can. Your work should consist of completing and moving forward.
Choose creativity over money
The changes you want to accomplish for yourself and your business should not include ‘spending money’. The Kaizen method does not need capital in order to succeed. Your creativity will bring low-cost alternatives to each of your problems. Creativity will be the solution for your improvements. You can only solve financial problems with money; however, with your creativity, every problem is solvable.
Ask for the help, wisdom and the opinions of others
The Kaizen method is not only about you. This method deals with everyone ‘as a whole’. Therefore, seeking others’ wisdom and opinion can help immensely for your work and the solutions of your problems. The knowledge of multiple people is always going to beat the knowledge of one. Keep that in mind. Do not hesitate to establish a collaboration environment.
Take on challenges
Do not run away from the problems and challenges you face. Superior knowledge, experience and wisdom can only be improved upon when you challenge hardships. That is why you should ‘run into’ those challenges, challenge yourself and come on top of them.
Ask ‘why’ five times in order to get to the root of the problem
This one of the practices Toyota followed. Asking ‘why’ times and answering each of the questions with a component answer. For example:
- Question 1: Why was the delivery of our product late?
- Answer: Because our servers crashed.
- Question 2: Why did our servers crash?
- Answer: Because the equipment is getting old.
- Question 3: Why is the equipment old?
- Answer: Because it was not replaced with the newer versions.
- Question 4: Why was it not replaced?
- Answer: Because the budget was not enough for improved equipment.
- Question 5: Why was the budget not enough?
- Answer: Because our revenue was down this month.
As you can see, a series of ‘why’ questions can reveal important problems and solutions for them.
Correct the wrongs immediately
If you see something is wrong, do not wait for another person to fix it. Correct every wrong you can find on the spot, right away. That way you will be enabling every situation (and thus, yourself) to adapt to change.
Encourage a positive work environment
Empowering your coworkers or your employees (if you are an employer) to speak, voice their concerns and support each other. Acknowledge everyone and anyone who is willing to participate in the problem-solving and decision-making processes. Open a space that supports contribution from everyone.
Always improve
The Kaizen philosophy’s key and the most important principle is to improve without an end. Always and endlessly, the Kaizen method encourages improvement.
The Different Types of the Kaizen Methodology
Even though the Kaizen method is based on a single concept of ‘continuous improvement’, it also provides a large framework. This framework consists of four different types of Kaizen strategy while using different tools and change methods.
- Kaizen Teian
This type of improvement is the individual improvement of those who are also helping to change the ‘whole’. Leaders, supervisors and employees all, should identify every opportunity for change and thus, improvement.
This constantly active and live acknowledgement for improvement on a daily basis can transform yourself and your workplace. In order to succeed in this type of Kaizen method, you should look for waste. Kaizen Teian focuses on the waste that you should remove from your life and work. Those forms of waste are:
- Defects
- Unnecessary and excessive parts
- Overabundance of production
- Workers who are unable to do their job
- Transportation or transfer costs
- Excessive movement (of equipment or employees)
- Talent which is not being put to use = This is the worst waste of all of them.
- Kaizen Events
This type of change, unlike Teian, deals with only a specific change and improvement. Even though they are shorter than the other types, they are much more demanding. Kaizen Events can go on for days or sometimes even weeks and they should be carefully planned by people in charge.
It should also be noted that even focusing on a specific improvement, can help for the change of the ‘big picture’. Each of the single events you and your team focus on should be aligned with the organization’s bigger and broader goals.
- Kaikaku
The Kaikaku method of transformation is somewhat different from the whole Kaizen method. While Kaizen focuses on improvement, Kaikaku demands radical, top to bottom changes.
The place that the Kaizen and Kaikaku method actually gets similar is the application of principles. The ten principles mentioned above for the Kaizen method, in fact, can be applied to the Kaikaku method of change as well.
It can be suggested that if you are seeking radical change for yourself and your business, apply the principles and begin with the Kaikaku method. Then, applying the Kaizen method for continuous improvements will perfect your working process.
- Kakushin
This type of change does not necessarily deal with challenges and problems. The Kakushin method of change changes the already in practice method with a new one. It is a commitment to a new way of doing things.
An example can be made that moving from writing letters on a piece of paper to writing emails on a digital device. Without a context, this change does not mean it is a good or a bad change. However, it is a change. And the Kakushin method of change uses brainstorming and analysis as its tools. These are the tools for a group of people who are willing to change what is already working. It is still challenging and demanding, but rewarding.
Additional Concepts of the Kaizen Methodology
The Kaizen Cycle
The Kaizen Cycle consists of a number of steps that follow each other and should be applied respectively. This cycle aims to create an environment that has its basis on continuous improvement. This systematic method includes seven steps and they are:
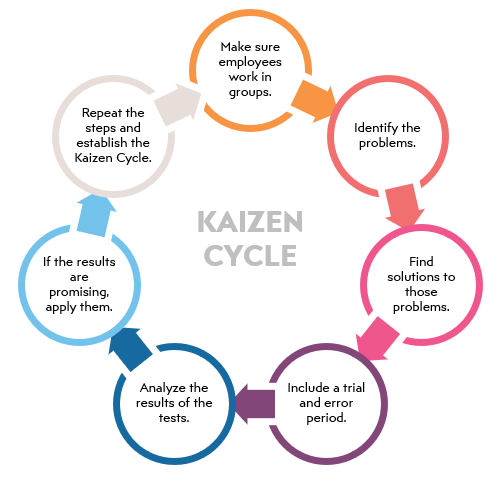
There is also one other Kaizen cycle as well. It is also known as the Shewhart or the Deming Cycle. The cycle consists of four steps: Plan, Do, Check and Act. It can also be abbreviated as PDCA and includes the same actions similar to the seven-step cycle detailed above.
The Kaizen 5S Framework
This part of the Kaizen methodology is used in order to establish an ideal workplace environment. Its main goal is to physically create a workplace that employees want to work in. The five different ‘S words’ are detailed in their original Japanese and their most common English translations below:
- Seiri – Sort: Organize your workplace. Keep what is necessary, eliminate what is not.
- Seiton – Set in order: Arrange all of your workplace items in order to easily access them.
Create an orderliness that is useful to you and your coworkers.
- Seiso – Shine: Keep your workplace clean. Pay close attention to cleanliness and tidiness in the workplace.
- Seiketsu – Standardize: Establish a systematic way of orderliness.
- Shitsuke – Sustain: Follow these disciplines.
Why the Kaizen Methodology Is Important
It is said that the only thing that keeps you from being successful is your mindset. Successful people have a ‘growth mindset’ that allows their intelligence to open up and improve. That makes the Kaizen method ever more important.
By applying the required disciplines and principles into your daily life and career at your workplace, you can create and improve upon:
- Your shared vision with your business (and coworkers),
- Your own skills, behaviors and attitudes,
- The collaboration between bosses and employees,
- The right mindset to allow you to develop, and
- A systematic way of thinking and understanding.
The Advantages of the Kaizen Method
- It creates a safer, more collaborative and more enthusiastic workplace,
- Establishes a stronger commitment from the employees to their work.
- Improves virtually anything, especially problem-solving and decision-making.
- Develops a sense of a team.
- Reduces unnecessary waste.
- Increases creativity, productivity and helps to achieve success.
- Diminishes the number of mistakes you, your coworkers and your organization makes.
- Helps each of the employees to only focus on their work.
- Establishes a stronger bond between the customer and the company.
- Boosts everyone’s morals in the workplace.
- Brings each of the employees a purpose for the work that they are doing.
- Allows employees to take charge and make their voices and concerns heard.
- Ensures a system open for improvements.
- Aims to succeed both in the short term and in the long term. This means that the Kaizen method is functional on a daily basis and also, on a yearly basis as well
- And last but not least, once you establish and apply its principles gradually, Kaizen methodology becomes an open-source for never-ending improvement.
How to Implement the Kaizen Method to Improve Your Business
Fortunately, the Kaizen method is extremely adaptive to different businesses, areas and cultures. This flexibility is also notable when it is applied to various companies with different goals, ways of working and systems. If you want to implement this method and start to improve your business, below you’ll find some of the recommended steps:
- Learn the method: The worst way to implement the philosophy is to do it without fully understanding it. Take some time and detailly understand and process what the method is and what it can bring to your company.
- Organize a seminar: Your employees, coworkers, supervisors, bosses, all need to learn and acknowledge the method at the same level. Otherwise, the method cannot succeed in an unequal work environment.
- Brainstorm with the employees: Create a brainstorming session in order to establish some of the problems your business is facing. The best way to improve is correcting the mistakes and solving the problems. The more people you gather and ask for their opinion, the easier it will be to identify the problems.
- Start with the most obvious challenges: No matter the problems and challenges your business is faced with are hard or easy, start with the most obvious ones. Because they will be the ones easier to produce solution options.
- Identify your waste: Locate the fields and areas your business produces the most waste. And try to create a plan or a system in order to cut and reduce that amount of waste.
- Take action in order to solve: Problems are not going to solve themselves; the waste is not going to reduce itself. You, both as an individual and also, as a team player, need to take actions and act accordingly to the method and the plan you have established.
- Repeat the method and always improve: Perhaps the most important suggestion for you to improve your business while implementing the Kaizen method is to stay consistent. If you implemented the Kaizen system, then stick to it. Repeat every time you need to solve a problem and cut waste.
Real-Life Examples of the Kaizen Methodology
The Kaizen method is one of the philosophies that is used both by individuals and companies such as huge conglomerates. Below, you can find some of the companies that use the Kaizen method in their day to day operations and long term plans:
Toyota
As it was mentioned in the previous chapters above, Toyota is not only one of the companies that use the method, but also it is one of the pioneers of the method. Toyota is responsible for making this method more known and popular for the entire world. Toyota uses this method in many different levels of production and manufacturing, from small to large operations.
Ford
Toyota is not the only car manufacturer that utilizes the Kaizen method. Ford also decided at the beginning of the 21st century that it will implement the method. Ford stated that it focuses on constant improvement for their manufacturing processes and workplace environment.
Nestlé
The food industry is one of the biggest sectors that focuses on implementing and applying Kaizen philosophy. Nestlé is one of the biggest companies in the world with products in many different fields. The lean production Nestlé most strives to accomplish is the reduction of waste.
Due to the fact that their products can affect the health of the people who are using (or eating) them, it focuses on diminishing the amount of waste. This waste includes both food and plastic waste. Nestlé promises that by 2025, their packaging will be 100% recyclable and reusable. The company invested $2 billion in order to achieve this. It also donates a lot of the food from their factories to pet shelters and people in need.
How the Kaizen Methodology and Someka Excel Templates Work Together
Kanban Board Excel Template
Someka’s Kanban Board Excel Template features an Automated Kanban Board and an advanced reporting mechanism with dynamic charts. The ability to look at each of the employees’ overall performances is an essential tool for you to track progress. If you prefer to use Google Sheets templates, then you can also download Kanban Board Google Sheets Template.
Also, its Dashboard section will update itself automatically with no need to enter the new data every time. By keeping track of the automatically generated results, you can start to improve your business. If you see that a task is not properly done, you can get in touch with the person in charge and start solving the problem. Kanban Board Excel Template is an essential tool to better your approach to the Kaizen system. You do not need to spend additional capital in order to succeed in the Kaizen system. Because the Kanban Board Excel Template is completely free.
Project Management KPI Dashboard
Someka’s Project Management KPI Dashboard lists the top 15 key metrics and performance indicators for you to improve upon. It takes away the time-consuming research process from you and does all the work. The business models it provides on various categories help you solve your problems in regards to time, budget, capital, spending and impact of your work.
The monthly and aggregate breakdowns it provides helps you improve your business and accomplish your goals. It focuses you to live in the present moment and create a positive work environment while it creates target values for your company.
It provides comparisons and trend charts so that you can fully acknowledge and realize the value of your company. Its interactive charts and customizable graphs will be incredibly useful while you implement the Kaizen method and apply its principles into your business.
The Someka templates work with the Kaizen method. The templates help you to enter the necessary data in order to support your Kaizen system and application of its disciplines and principles.