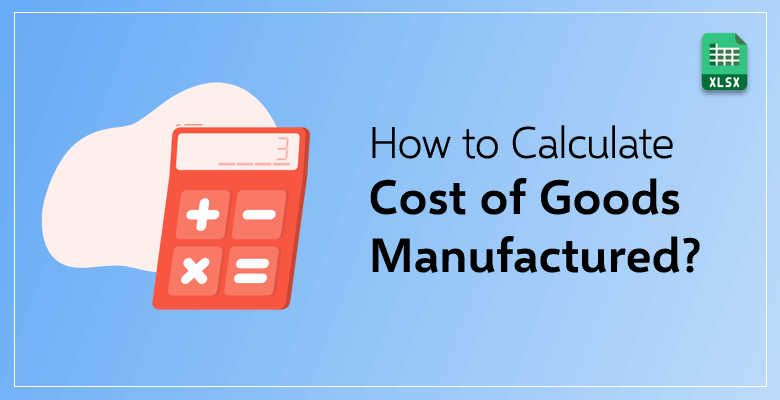
How to Calculate Cost of Goods Manufactured?
Almost everything has a cost; some are calculable and some not. In production, costs are luckily suitable to calculate in mathematical ways. Calculating costs is the first step of managing them.
Costs are crucial in terms of the overall production process and profitability. Calculating the costs of goods manufactured is a guide for many companies to manage their expenses.
What Is Cost of Goods Manufactured (COGM)?
Cost of goods manufactured, also known as COGM, is the accounting term referring to the total production cost of a company in a certain period of time. That includes any expenses from the manufacturing products to the goods completed; such as raw material costs, work in progress and labor expenses. COGM could be defined as the overall picture of how much a business spent to turn their inventory into the finished products.
Why Is Cost of Goods Manufactured Important?
One thing is for sure; money is one of the most significant constraints for any business. Knowing how to manage it allows companies to enhance their conditions and eventually make their business better. Cost of goods manufactured is the proper way to understand how high or low production costs are. Companies, in that way, have the chance to evaluate their expenses versus their revenue and optimize the overall production costs.
Imagine a standard production process. Different expenses play roles in the process and result in either profit or loss. If the company has a clear understanding about the costs in production, then we can mention dealing with loss or evaluating the profit. By knowing the costs of goods manufactured, companies focus on planning and pricing strategies. They can cut off the expenses that might be unnecessary, substitute the materials with the cheaper ones or make some changes that make the production more profitable.
We can list some of the benefits of COGM as follows.
- General view about production costs
- Minimizing losses and expenses
- Maximizing profitability and income
- Effective usage of resources
- Developing pricing strategies
Difference Between COGM and COGS
Cost of goods sold (COGS) is the cost of selling products, in other words the cost of finished inventory ready for sale. If we get more specific; finished inventory is any type of finished product, goods or services, that is ready to be delivered to the customer.
Although COGM and COGS are both included in the product cost planning process, the main difference between these two is that COGS additionally involves other expenses regardless of manufacturing. Whilst COGM is about calculating material costs and production overhead; COGS includes cost of goods manufactured together with other costs such as sales, shipping or labor costs. COGM could be counted as a way station in the COGS route.
COGM Formula
Now we can go deeper and find out how to calculate the cost of goods manufactured. The COGM formula is basically formed as calculating the total manufacturing costs, adding the beginning WIP (work-in-process) inventory and subtracting the ending WIP inventory from this sum.
COGM = Total Manufacturing Cost + Beginning (WIP) Inventory – Ending WIP Inventory
Total manufacturing cost refers to the sum of direct material cost, labor cost and the manufacturing cost. Let’s see step by step how to reach that cost and then how to involve the inventory in calculation.
Step 1: Determine the direct materials
Direct materials are the raw materials that are used in production. The raw materials held at the beginning of the production could be partially left unused at the end of the process; which is later called ending raw materials. Also, do not forget that there could be raw material purchases in the meantime. To calculate the direct materials, add beginning raw materials to the purchases and subtract the ending raw materials from the total amount.
Take a look at the example in Excel below, and see how the direct materials are calculated. Certain costs and related information of a production company are given in the worksheet:
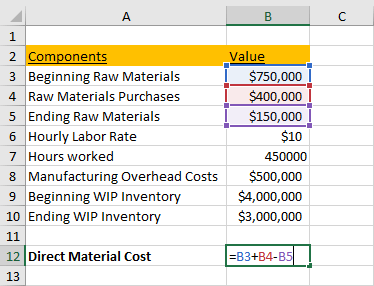
Beginning raw materials cost is stated as $ 750,000, purchases cost is $ 400,000 and the ending raw materials cost is $ 150,000. All you need to do is calculate the direct material cost according to the formula; which in Excel you can do it among the relevant cells.
Direct Material Cost = Beginning Raw Materials + Purchases – Ending Raw Materials
$750,000 + $400,000 – $400,000 = $1,000,000
Step 2: Find out the cost of all labor used
Direct labor cost is calculated by multiplying the total worked hours and the labor rate per hour. It is more simple to find it compared to direct materials; hours rates are generally fixed and with the information of how many hours are worked in total, the direct labor cost is easily calculated.
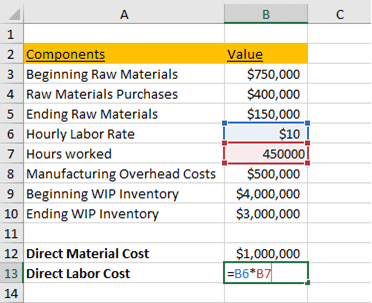
In this example, labor rate is given as $10 per hour and the total worked hours are 450,000. Multiplying these two values gives us the direct labor cost.
Direct Labor Cost = Hourly Labor Rate * Hours Worked
$10 * 450,000 = $4,500,000
Step 3: Add the manufacturing overhead cost
Direct materials cost and direct labor cost were calculated; there is only the manufacturing overhead cost left to reach the total manufacturing cost.
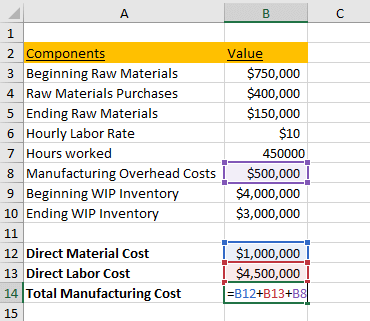
Adding overhead costs to the already calculated direct material and labor costs, total manufacturing cost is reached.
Total Manufacturing Cost = Direct Material Cost + Direct Labor Cost + Overhead Cost
$1,000,000 + $4,500,000 + $500,000 = $6,000,000
Step 4: Add the beginning work-in-progress inventory
First part of the COGM formula is done. Next step is to add the beginning work-in-progress inventory to the sum. It is already given straightly in the Excel sheet.
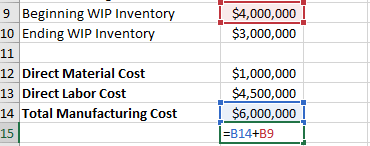
Adding beginning WIP inventory to the total manufacturing cost, the new sum is obtained.
$6,000,000 + $4,000,000 = $10,000,000
Step 5: Subtract the ending WIP inventory
Only one step left to finally reach the cost of goods manufactured. The last thing to do is subtracting the ending work-in-progress inventory.
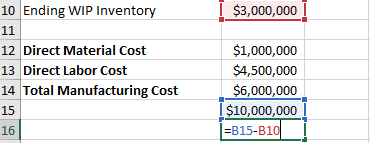
= $10,000,000 – $3,000,000
= $7,000,000
At the end of the calculation, you can see that the result is $7,000,000.
What Is Manufacturing Overhead and What Does It Include?
Manufacturing overhead is a part of the COGM formula; more specifically one of the components in the total manufacturing cost part. However, what should we include into manufacturing overhead is a complicated matter and doesn’t have a certain answer.
Manufacturing overhead consists of indirect product costs that are incurred in manufacturing facilities. Even though they are necessary for products, they don’t directly affect the final product. Some indirect costs could belong to the cost of goods sold since they might be associated with the selling products. Therefore, deciding where to put them might be difficult. Handling costs, storage costs, rent or transportation costs; should we include them into overhead cost or COGS? Or are they fixed costs?
Rent cost for instance is under the overhead cost only if it is the rent of manufacturing facilities. If it is a general office rent regardless of manufacturing, then is not included in overhead cost. Transportation on the other hand could be considered as either the shipping of the goods sold or the products purchased. Shipping cost is a part of COGS, but paying the transportation of the purchasing product will be included under the cost of goods purchased. The key point is to decide whether these costs are incurred on a manufacturing specific basis. Electricity and gas are normally fixed costs and monthly expenses just like rent. However; they become manufacturing overhead costs if they are allocated to the units manufactured. Electricity systems work as usual and aren’t affected by how many units products are processed, but if the electrical energy is being used with a higher volume for a particular unit; it starts to seem like a manufacturing overhead cost.
So, if an indirect production cost is related to manufacturing facilities anyhow; then it is counted as a manufacturing overhead cost. Electricity, gas, maintenance, depreciation, factory supplies, rent and taxes of the manufacturing facilities are some of the examples of manufacturing overhead cost.
Examples of Costs of Goods Manufactured
See some examples of companies below and how COGM calculations are made.
Example 1:
The Choco, a chocolate factory, spends $5,000 on their direct material and $3,000 on their direct labor. Manufacturing overhead cost is $2,500. The Choco began the year with a $4,000 amount of beginning work-in-process inventory. The ending work-in-process inventory is $2,000. Find the cost of goods manufactured:
Total Manufacturing Cost = $5,000 + $3,000 + $2,500 = $10,500
COGM = $10,500 + $4,000 – $2,000 = $12,500
Example 2:
The Silk is a textile factory and began the year with the inventory cost of $70,000. The factory’s direct material cost is $100,000 and the manufacturing overhead cost is $60,000. The hourly labor rate they pay for each employee is $10. There are 100 workers and each working 500 hours. The Silk ends the year with $30,000 ending work-in-process inventory. Calculate the cost of goods manufactured:
First, we need to reach the direct labor cost by multiplying what is given
Direct Labor Cost = $10 * 100 * 500 = $500,000
Total Manufacturing Cost = $100,000 + $500,000 + $60,000 = $660,000
COGM = $660,000 + $70,000 – $30,000 = $700,000
FINAL WORDS
Accounting is sometimes complicated, yet it is an opportunity to record highly critical information. Because when money is involved every calculation needs to be extra carefully done. As with many other cost accounting operations, the cost of goods manufactured requires being aware of each component, to determine them right and include them to the calculation accordingly. Learn what is COGM in depth, figure out why it is important and examine the steps to calculate it for your company.